Overview
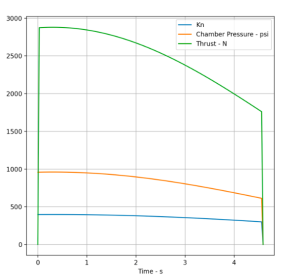
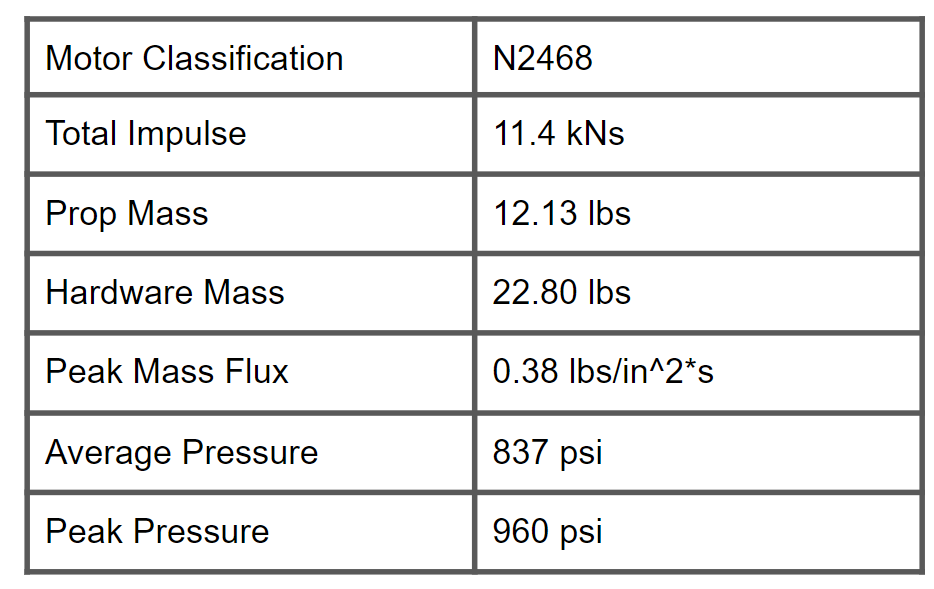
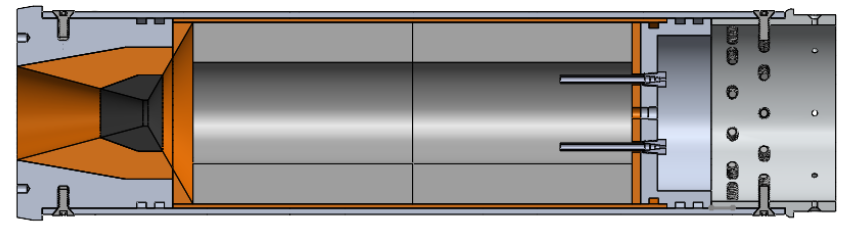
Grain Geometry

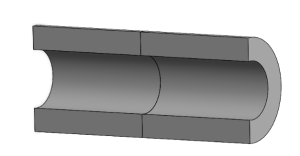
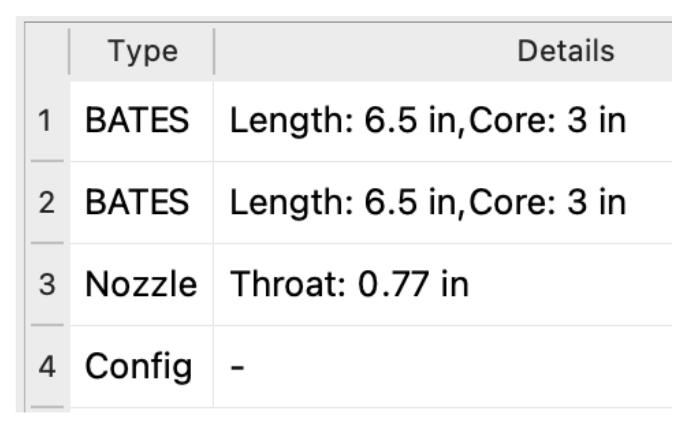

Went with cylindrical geometry, less complex than booster motor
Nozzle
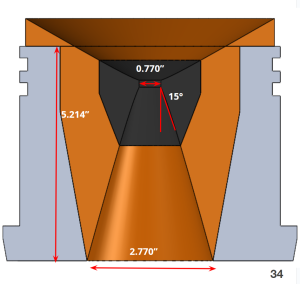
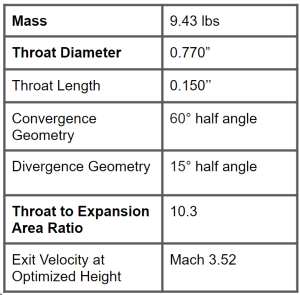
Withstand 2*max operating pressure of the chamber
Attach securely to booster case
Support the fin can under high acceleration
Optimized for 14350 ft above ground level (sum of 2/3 of height difference from ignition to burnout and ignition
Materials
Aluminum 6061-T6
Canvas phenolic
Graphite
Decided to go with a concave convex nozzle rather than a bell nozzle like on the booster
Two part phenolic seemed smart in design, but in practice was difficult to manufacture
When making the top phenolic ring I got chastised by Todd for a completely infeasible design (was somehow able to manufacture it but it was super sketch, just had to face 500thou )
In the future it would be much better to make the phenolic into one whole part rather than two pieces

Case
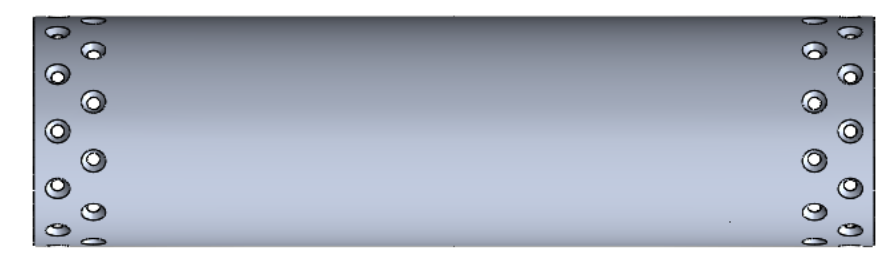
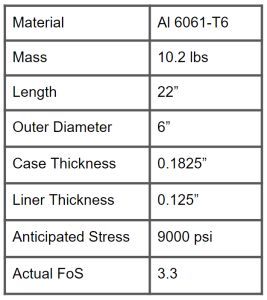
Requirements
Withstand 960 PSI during burn
Withstand 1440 PSI for twice the burn time during hydrostatic test*
Utilize a FoS of 2*
Hoop Stress Approximation
P = pressure
R = radius
t = case thickness
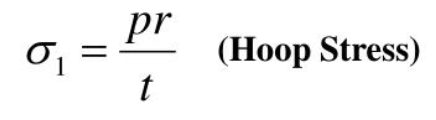
FRR, FC and Bolt Calcs
Safety Margins
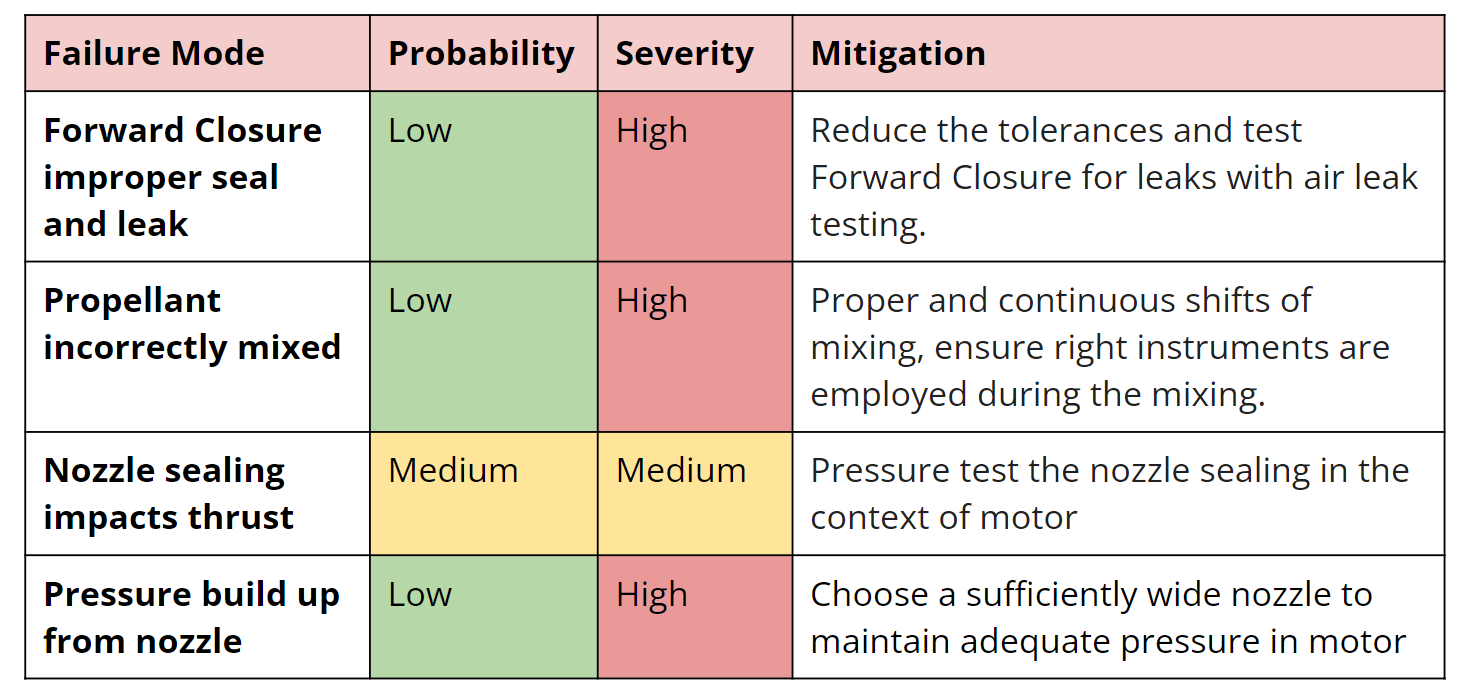
{"serverDuration": 139, "requestCorrelationId": "4644553e405a0a28"}